Why and how do we electroplate? The transformation of goods made from base metals into higher-value commodities using precious metals
A look at the pros and cons of electroplating
Why do we electroplate?
Tragically there is no such thing as alchemy or magic when it comes to metals. If we could use alchemy, we would all be driving around in 24k gold cars. Whom amongst us would not want the ability to change common, low-value base metals into precious, rare metals? So magic is unfortunately out of the question but, the simple chemistry used in electroplating could be the next best thing.
Electroplating gives us the ability to use common or garden electricity, a sacrificial metal and a few cheap and readily available chemicals to transform an everyday metal, such as copper or steel, with a thin layer of another, much more desirable metal, such as chrome, gold or even platinum.
Electroplating gives us the ability to protect metals that readily oxidise (rust) as well as enhancing the metals appearance and is also used to cheaply transform inferior products into having the appearance of expensive products. For example, a solid gold watch can run from $10,000 upwards, whereas a gold plated watch can be yours for $70-80.
It is not a new process, electroplating was patented for the first time in 1840, the process is actually older than this date with the first experiments dating all the way back to 1805. That is 213 years ago.
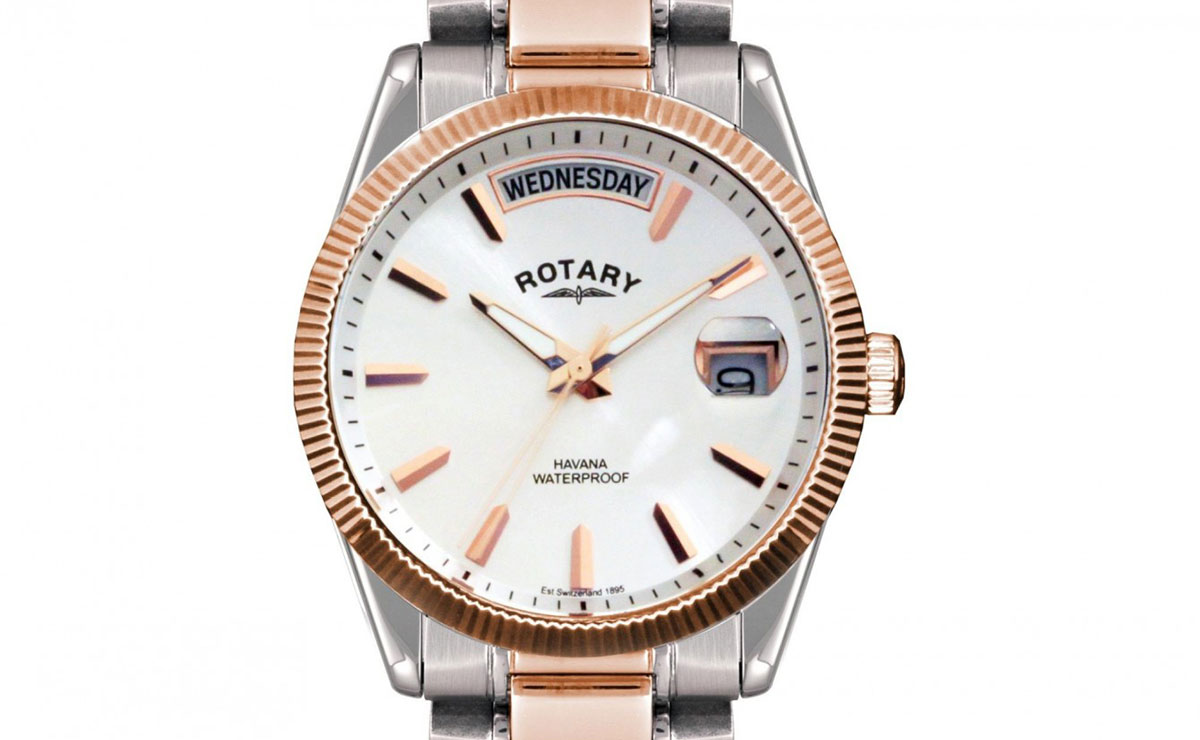
Rotary Havana Two tone Rose Gold plated watch
The benefits of electroplating
Thanks to these abilities, electroplating has found its way into many other everyday areas. Some of the benefits of electroplating include the following,
- Electroplating produces a beneficial protective barrier that can help protect the substrate against harsh environmental conditions. The substrate can be metal or plastic.
- Electroplated parts that can come into contact with harsh environmental conditions can last longer therefore being cost-effective.
- Electroplating is spectacular at enhancing the appearance of the surface of a metal and because of this jewellery is often electroplated with an extremely thin layer of precious metal to make it more appealing and attractive to potential customers.
- Jewellers can sell their electroplated products that have the appearance and lustre of pure gold at a significantly lower price point than solid gold.
- Electroplating will improve electrical conductivity. Electroplating electrical components with pure silver will help enhance electrical conductivity, making electroplating a precious and useful industrial process for the manufacturers of electronics and electrical components. The electrical device you are reading this article with is an excellent example of this process.
- Electroplating is resistant to heat. The electroplating process using gold or zinc-nickel are capable of withstanding very high temperatures.
- Electroplating with these metals will protect the plated engine parts and components from the high temperatures produced by the internal combustion engine. The protection offered given these electroplated parts will improve their lifespan.
- Electroplating gives a smooth and uniform surface finish. It will fill pits and dings in a surface that has corroded. This means that a surface the has rust pitting on it or scratches can be sent back to the electroplating factory for refinishing. After the part has been re-plated, it will look as good as new.
- Electroplating can also be used to prevent permanent tarnishing. Electroplated silver items are an excellent example of this. Silverware will keep its shiny appearance and are readily cleaned if they do tarnish. This helps silver plate retain its value over time.
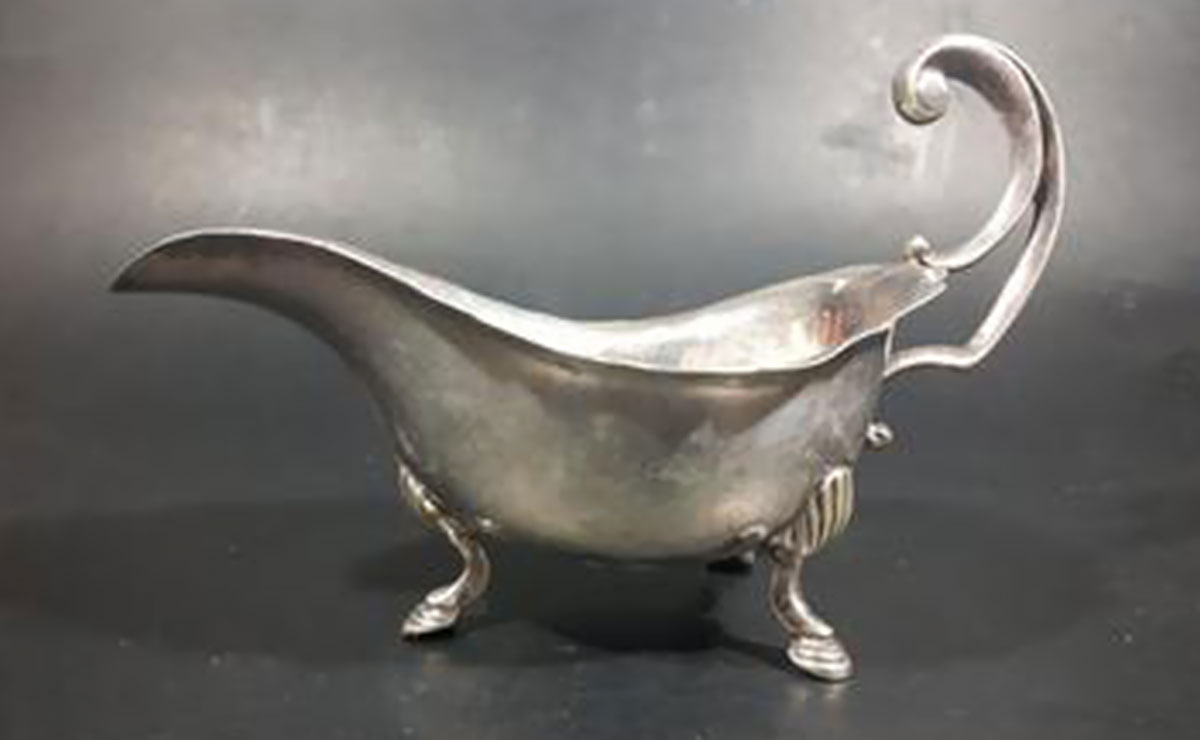
Antique Victorian footed Gravy Boat/Pourer in electroplated silver. Sold via Treasure Valley.
Electroplating process
The process of electroplating involves passing an electric current through a solution called an electrolyte. An electrolyte is defined as ‘a liquid or gel which contains ions and can be decomposed by electrolysis, e.g. that present in a battery.’
The first step after cleaning and preparation of the item to be plated is to dip to electrodes into the electrolyte and to connect them into a circuit with a power supply. In our case, the power supply is electricity from the mains, but you can use a battery if you have to.
These electrodes are called terminals.
By passing electricity through the terminals, you complete the circuit, freeing the desired metal ions from one terminal and depositing it over the surface of the other terminal. So one terminal will be composed of the metal you wish to plate with, and the other terminal will be the part to be plated. As I said, almost magic.
The disadvantages of electroplating
Acids used in electroplating gold must be continuously adjusted so as not to cause the formation of hydrogen cyanide in the electrolyte, at ph values above eight, the fumes from the hydrogen cyanide will become lethal. Because of this wastewater and sludges produced in electroplating constitute a significant risk to people and the environment due to the cyanide contained in the slurry.
Cyanide is lethal to humans if taken orally. A single dose of cyanide may produce acute poisoning and rapid death. The extent of metal and cyanide pollution in the untreated wastewater of an electroplating factory without modern treatment systems, if discharged into sewers or watercourses has a high potential to harm human life as well as aquatic life including birds, fish and reptiles.
In a very modern factory with mandated treatment facilities, the quality of water is acceptable but never ideal.
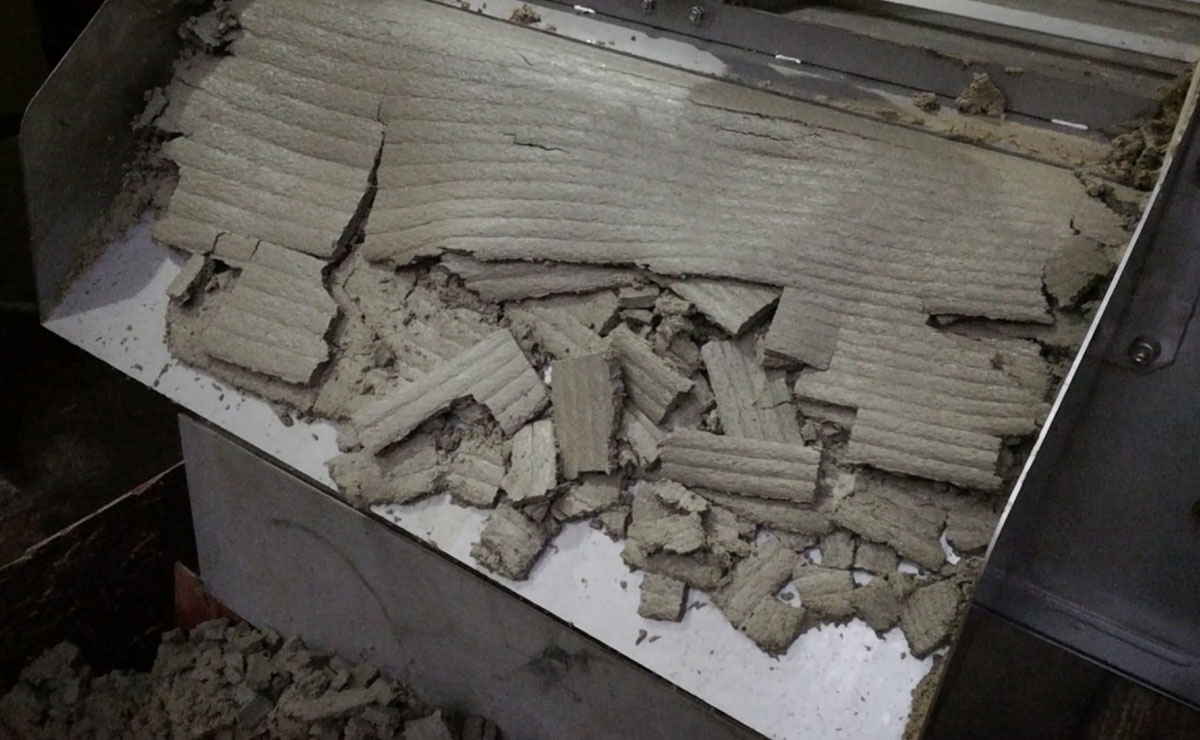
Electroplating sludge. Image by Sludge Dewatering Press Lifeng Enviromental
Because of the waste products, it is difficult to open new electroplating factories. This means that most facilities in the USA are ‘grandfathered in’.
Electroplating has been superseded by other much cleaner and much more environmentally friendly technologies such as PVD which produce no wastewater or poison-laden sludge.