22 Bishopsgate – The process of designing and building a skyscraper using the foundations of a previous design.
State of the art technology encompassing steel, glass and concrete.
I find fascinating in the construction process of any skyscraper that every piece that has been installed on site, has made a long journey from where it has been fabricated to its final position in the configuration of the building. In the construction of 22 Bishopsgate for example, some of the stone came from Italy, steel arrived from China, the façade panels came from Germany, the BMUs (those mechanical arms where the people that clean the façade hang from) come from Spain, some furniture in the lobby was produced in France…
Every beam, column, concrete block, door, toilet, handle, signage, has been fabricated and installed by a human being, and this proves that, still nowadays, construction is very much a handmade process. Of course some tools are still required to manage the heavier pieces of construction, but even then those tools, are actively controlled by people.
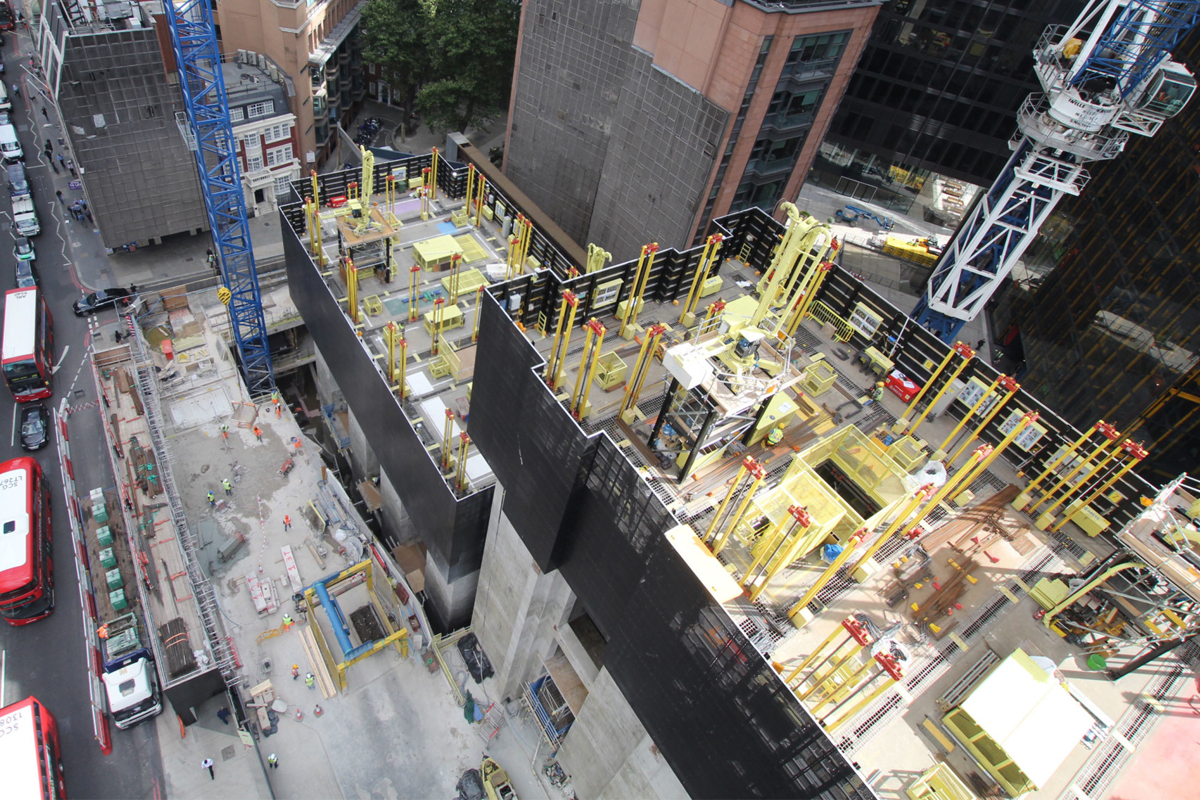
View of the building site from above, we can see how the multiple pieces of construction equipment are organized to allow for the builders to move around the site. 22 Bishopsgate designed by PLP Architects, construction by Multiplex.
Photo from Careys Design Team by Lobster Pictures.
A great team effort
The design team of a project of this scale, at peak times, probably involved around 25 architects, 8-10 structure engineers, some more Mechanical, Electrical and Public Health engineers, Landscape architects, Lighting Designers, Security Consultants, Façade Access Consultants, Fire Engineers, Planning Consultants, Visualization artists, Wayfinding consultants to name a few. Besides all these designers, there is an even bigger team working for the main contractor company full time on the project, and then there are the countless subcontractor companies involved in the construction.
And if all these people weren’t enough, an even bigger greater amount of people are involved in constructing the building with their own hands and their construction equipment. In order to finalise the job on time it has been required to have people working 24/7 and this implied having 1200 people spread around the site at once during construction peak times.
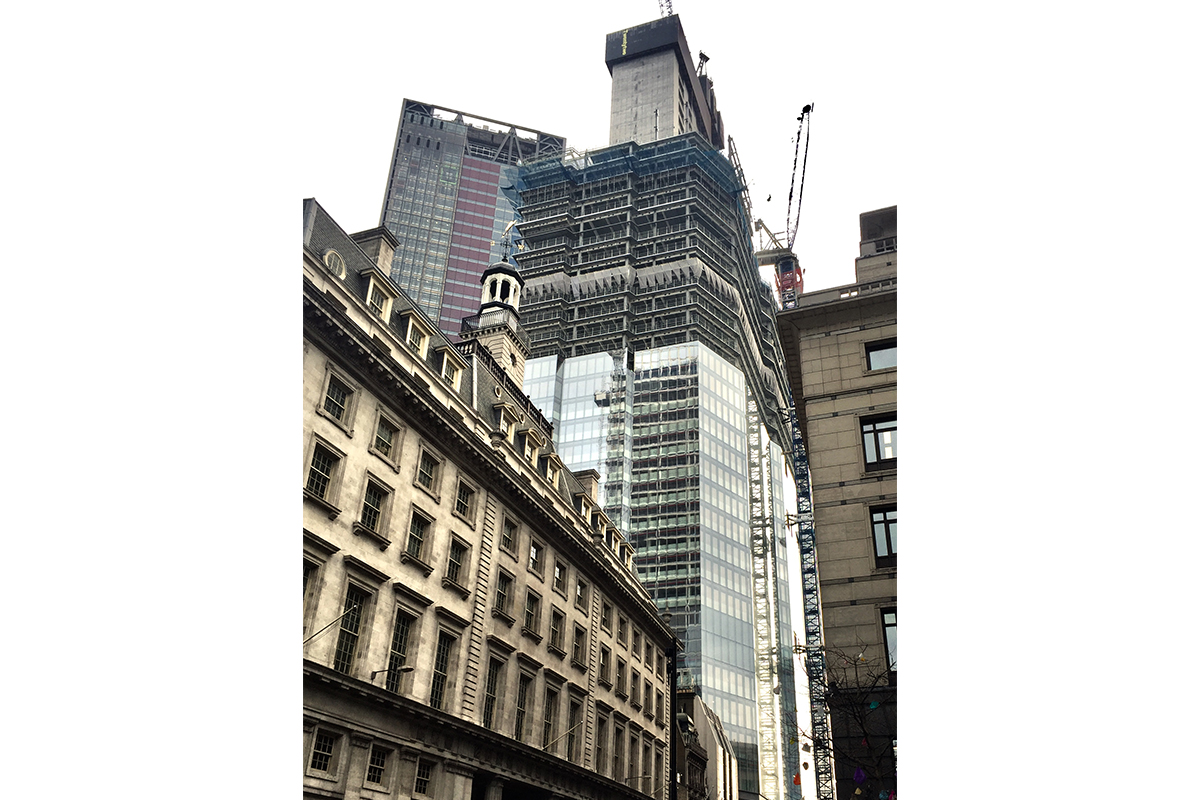
Images of 22 Bishopsgate at different stages of the construction process, we can see how the three main parts of the building: core, slabs and façade progress in a stepped sequence over time.
Photograph by Antonio Moll
Top down construction
Construction began by demolishing the existing core and cutting those parts of the basement slabs that were required to build the new core and to facilitate the construction of the new design. It was decided to use the Top Down construction methodology. This technique is often utilised to shorten the duration of the construction programme and the associated money that comes with it. It consists in starting to build the core from an elevated level, in this case from the ground floor. This way, construction can progress simultaneously above and below ground.
Temporary structural elements are built to support core. These usually occupy less space than the final configuration of the core walls would thus freeing space underneath and facilitating the execution of the works required below ground. These temporary structure elements are removed at a later stage accommodate the underground portion of the core.
This way, the works above ground level can start earlier because it is not needed to wait those 3-4 months required for the core to reach ground floor – in the case the core was built using the traditional construction method starting from the lowest basement and foundation level. Apparently, at one point during construction, the core reached level 20 before its basement levels and foundation had been built. This is an impressive feat of engineering without any doubt.
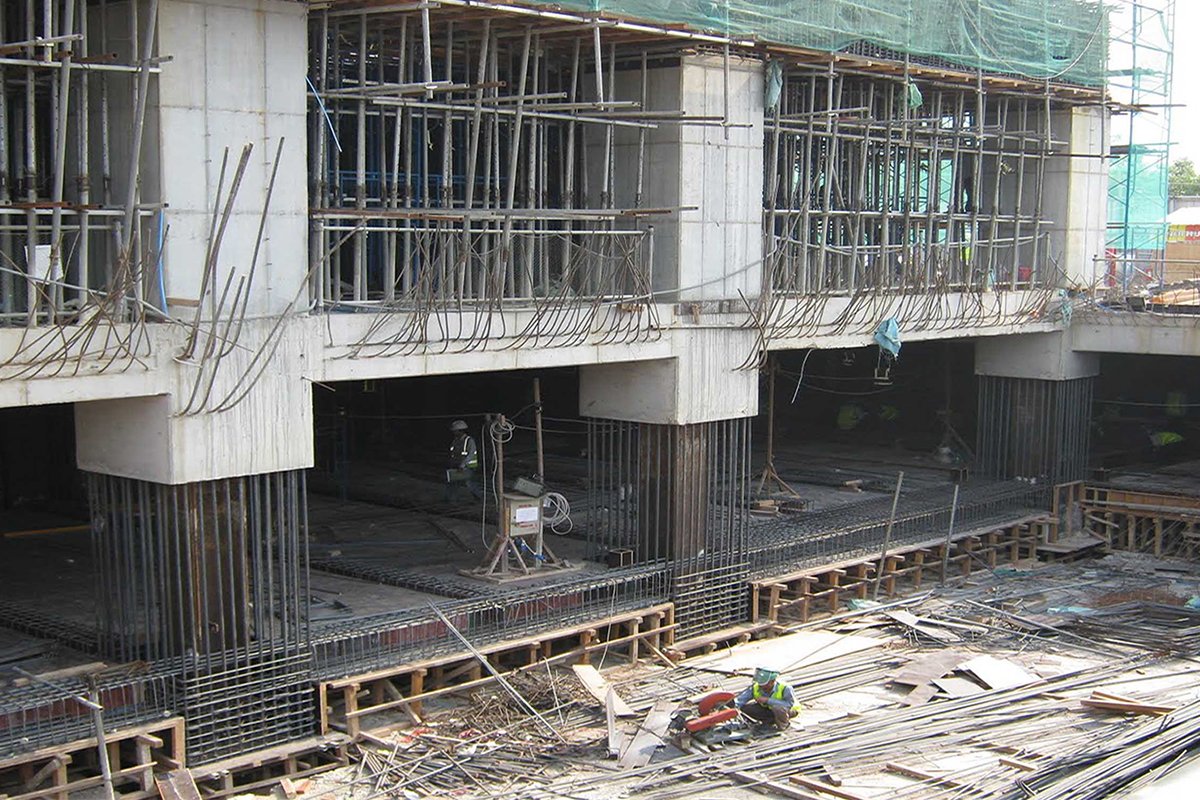
Image from a building site which is being built using the top down construction method, the above ground structure is already finished while the lower part is still due to be infilled with concrete.
Image from Engineering Discoveries.
A skyscraper structure
The structure of 22 Bishopsgate is primarily divided in two parts, the central core made of concrete and the surrounding beams and columns which are fabricated of steel. The gigantic core – its footprint at the ground floor is roughly 60 x 15 meters – is formed by walls that reduce their thickness as they rise to the top floors, accommodating the reduced structural demands of the upper levels in comparison to those of the lower ones. At the same time the footprint of the core also reduces as a result of the lesser number of lifts and services that reach the top floors. This is not uncommon in high rise structures.
The design coordination process of the structure of a building requires a continuous back and forth. Architects and engineers exchange drawings, mark-up comments and hold meetings on a weekly basis during the busiest times of the coordination. This exhaustive dedication is required to check progress and make sure that scheduled programme is met.
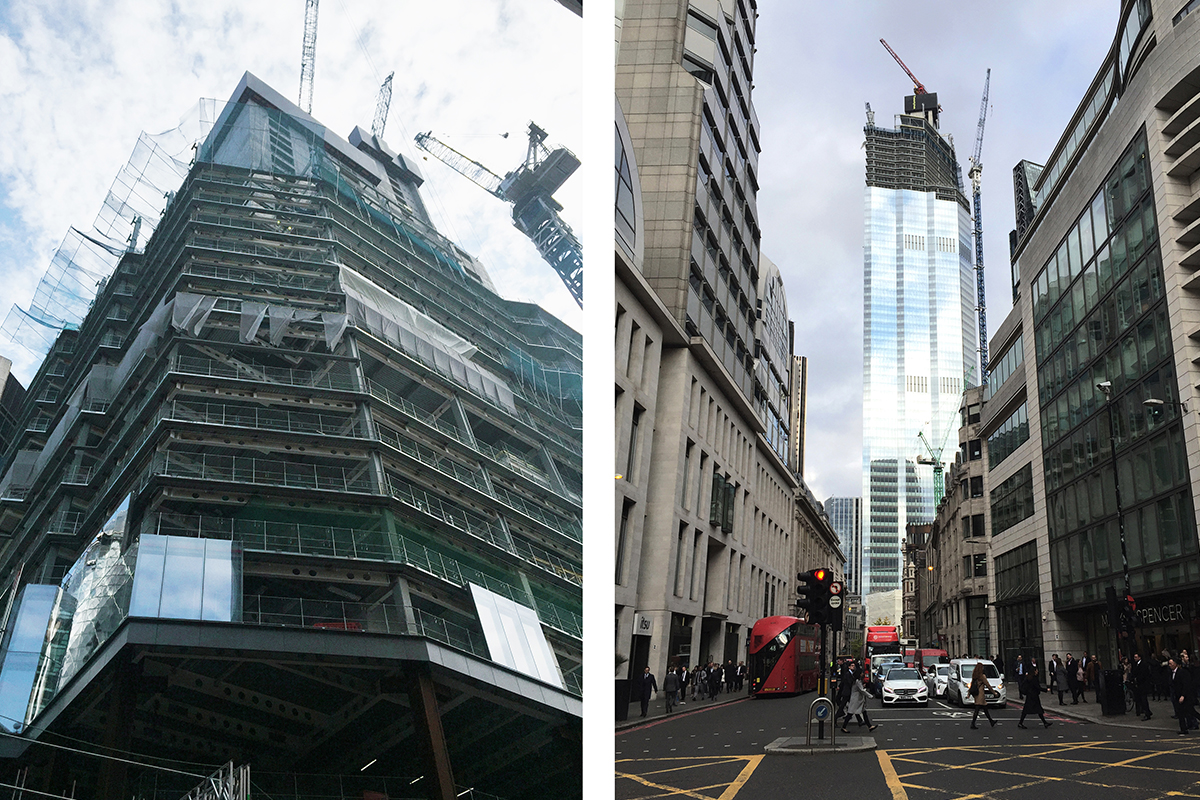
22 Bishopsgate during different stages of construction. We can observe the sequence in the construction of the main elements of the buildings: the core, the steel frame and the cladding.
Photographs by Antonio Moll
A bit of technical knowledge
The most interesting concepts of the overall functioning of the structure from my point of view are the lateral stability and the axial shortening.
We should understand lateral stability as the resistance of the building to fall sideways due to the action of the wind hitting the building, or an earthquake in a seismic area- luckily London is not one of these. In order to respond to the pushing forces of the strong winds affecting the top of the building at such height, the engineers designed a series of trusses that play the role of outriggers located at levels 25 and 41. These are gigantic steel structures that span from floor to ceiling and tie back to the concrete core. The main role of these structural elements is to restrain the building, helping it to stand still when the wind tries to bend it down.
On the other hand, the axial shortening affects the structure of a skyscraper vertically. As construction progresses and the building reaches higher levels, the entire building sinks marginally into the ground, we are talking of dimensions in the range of a few centimetres. And not only this, the structure also compresses and shrinks gradually due to the effect of the increased weight that it has to support as work progresses on site and more material and weight is added to the building. All of this has to be taken into account when designing the structure. Explaining it in a very simplistic way: columns are designed longer than required so that after the axial shortening occurs, they reach their nominal length so each floor remains at the exact level defined in the architectural project.
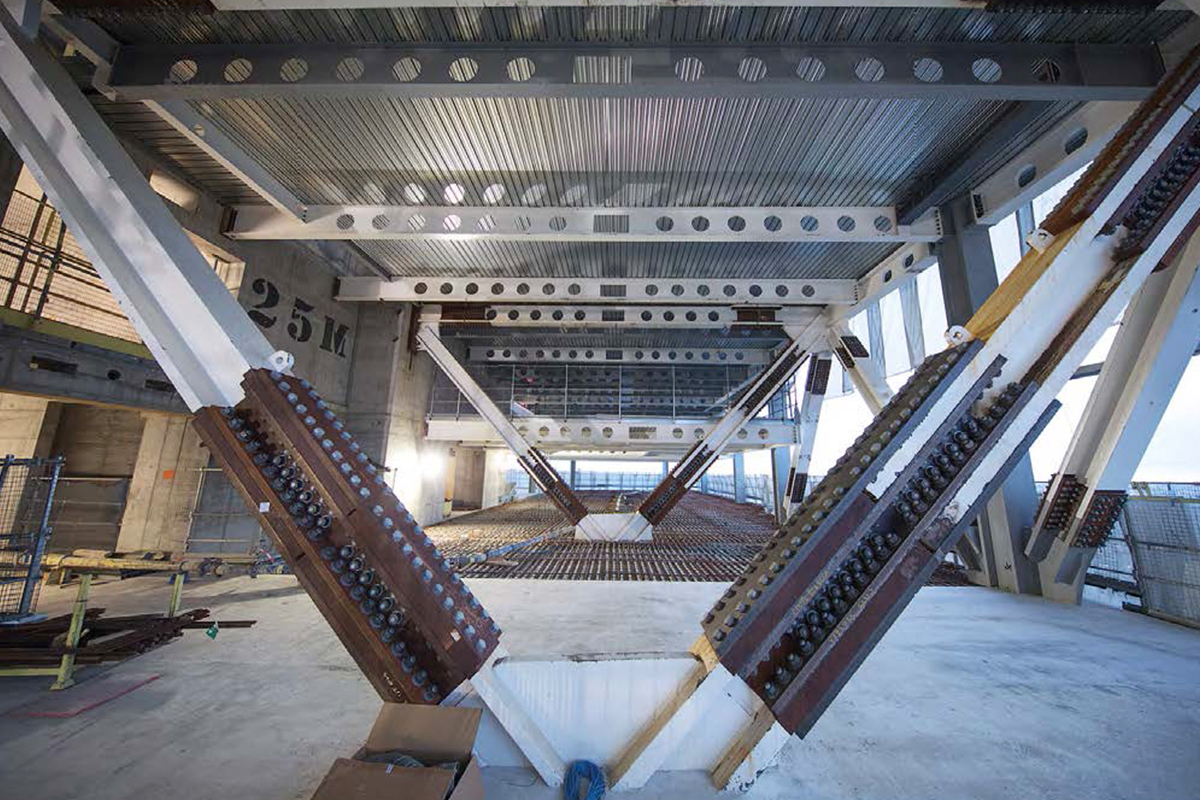
View of the outriggers at level 25, these structural elements provide lateral stability to the skyscraper and impede the lateral movement due to the action of wind.
Façade Panels
The skin of the building is composed of a double layer of glass with a pressurized cavity in between. This type of cladding is named under the acronym CCF which stands for Closed Cavity Façade. The entire envelope is divided in single panels, each of them of around 4m high and 1.5m wide that come from the factory ready to be installed in place. Each of the cavities of each panel is fed by a constant flow of air that keeps it over pressurized, like a balloon, improving the thermal performance of the façade.
The glass employs the latest technology to achieve a great level of transparency from the inside and a beautiful white reflection when seen from the outside that makes the building vanish, reflecting the surrounding environment and changing the tone as the different tones of daylight strike on the different faces of the building.
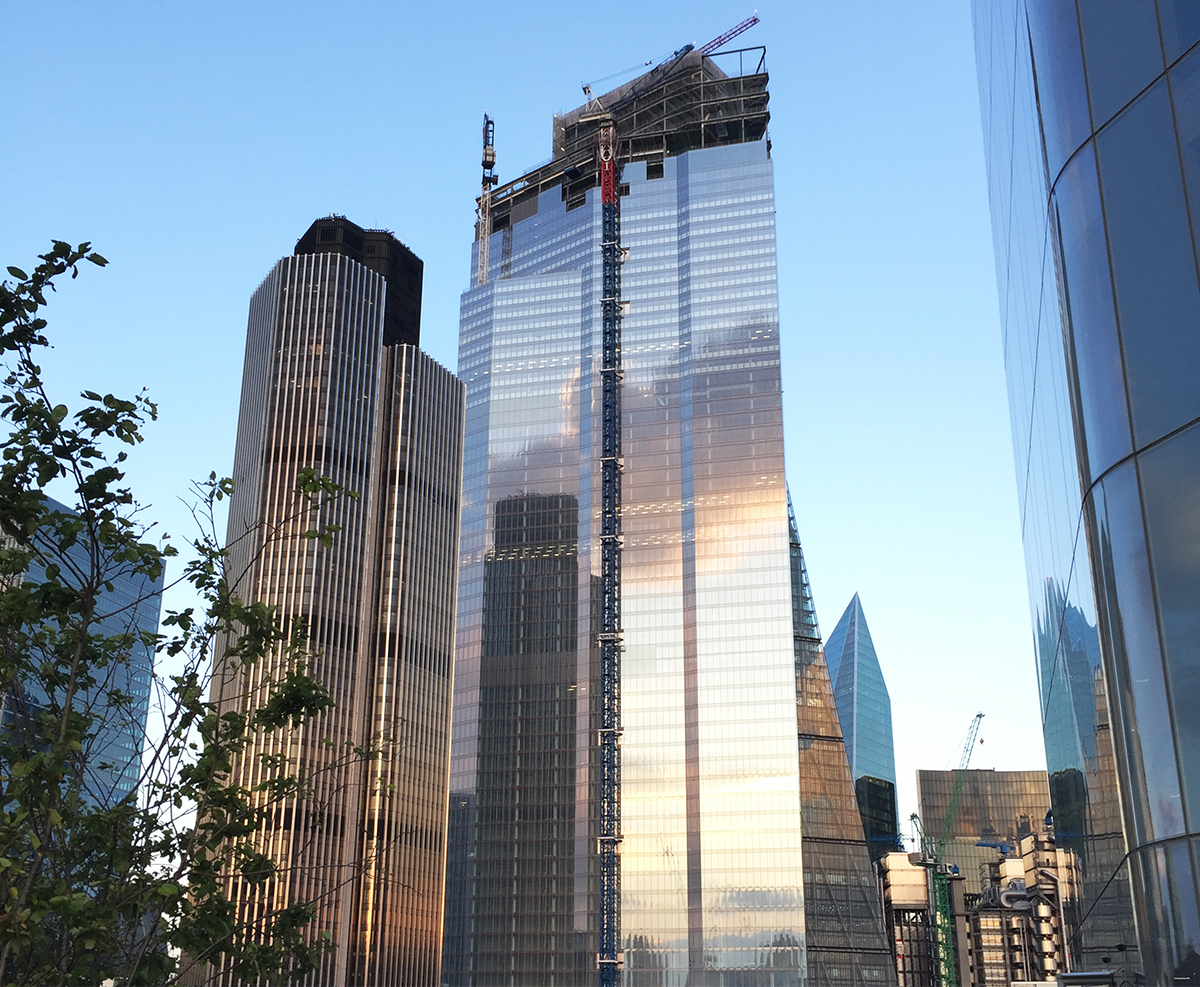
Tower 42 reflected on 22 Bishopsgate. The state of the art technology of the glass makes it vanish in between the surrounding environment.
Photograph by Antonio Moll.